Test Facilities
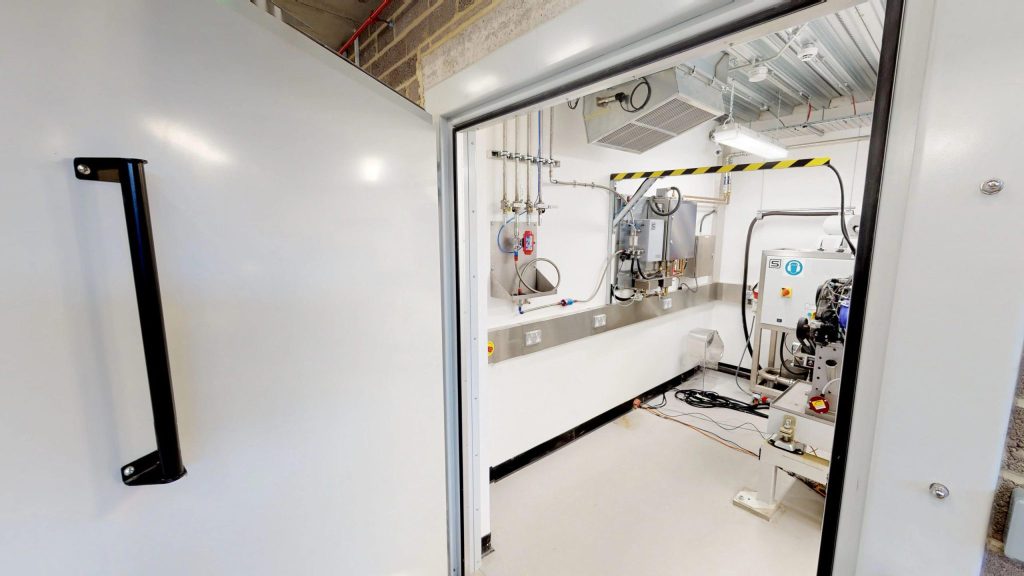
Engine Calibration
Using an engine dynamometer is crucial for accurate EFI calibration, as it allows testing across all engine loads and RPM ranges. Calibrating combustion engines is inherently complex and detailed. Unlike static propeller testing, which is limited to certain regimes, a dynamometer enables a full spectrum analysis. Moreover, it measures engine friction and evaluates the performance of auxiliary devices like pumps and alternators. Simulating in-flight engine loads in a static thrust bench is challenging due to the significant RPM increase caused by aircraft speed. The PowerDyne engine dynamometer provides UTG with exceptional capability to calibrate, characterize, and test small propulsion systems for unmanned aerial vehicles, ensuring precise and reliable performance. This setup, featuring gas analyzers, a precision fuel flow meter, and a temperature chamber, ensures reliable determination of optimal spark advance, fuel delivery, and other calibration settings at every mapping point. Combined, these tools provide unparalleled accuracy in engine calibration, enabling precise adjustments and performance optimization.
Engine Endurance
Our endurance testing facilities allow remote engine operation for comprehensive endurance tests, equipped with features like an air exchange fan, dual cooling fans, automatic fire suppression, and 24-hour unattended endurance run monitoring. These tests are essential for validating UAS propulsion system designs to meet the designated TBO (time between overhauls), evaluating not just the engine but also the fuel system, isolation mounts, wiring, and starter generator systems. Additionally, our engine test room provides a controlled environment for engine testing, featuring two centrifugal cooling fans for continuous cooling even under full throttle conditions. An air extractor ensures oxygen replenishment, while engine operation is remotely controlled from a PC outside the chamber via extended communication cables.
